The Crucial Role of a Die Casting Mold Company in Modern Manufacturing
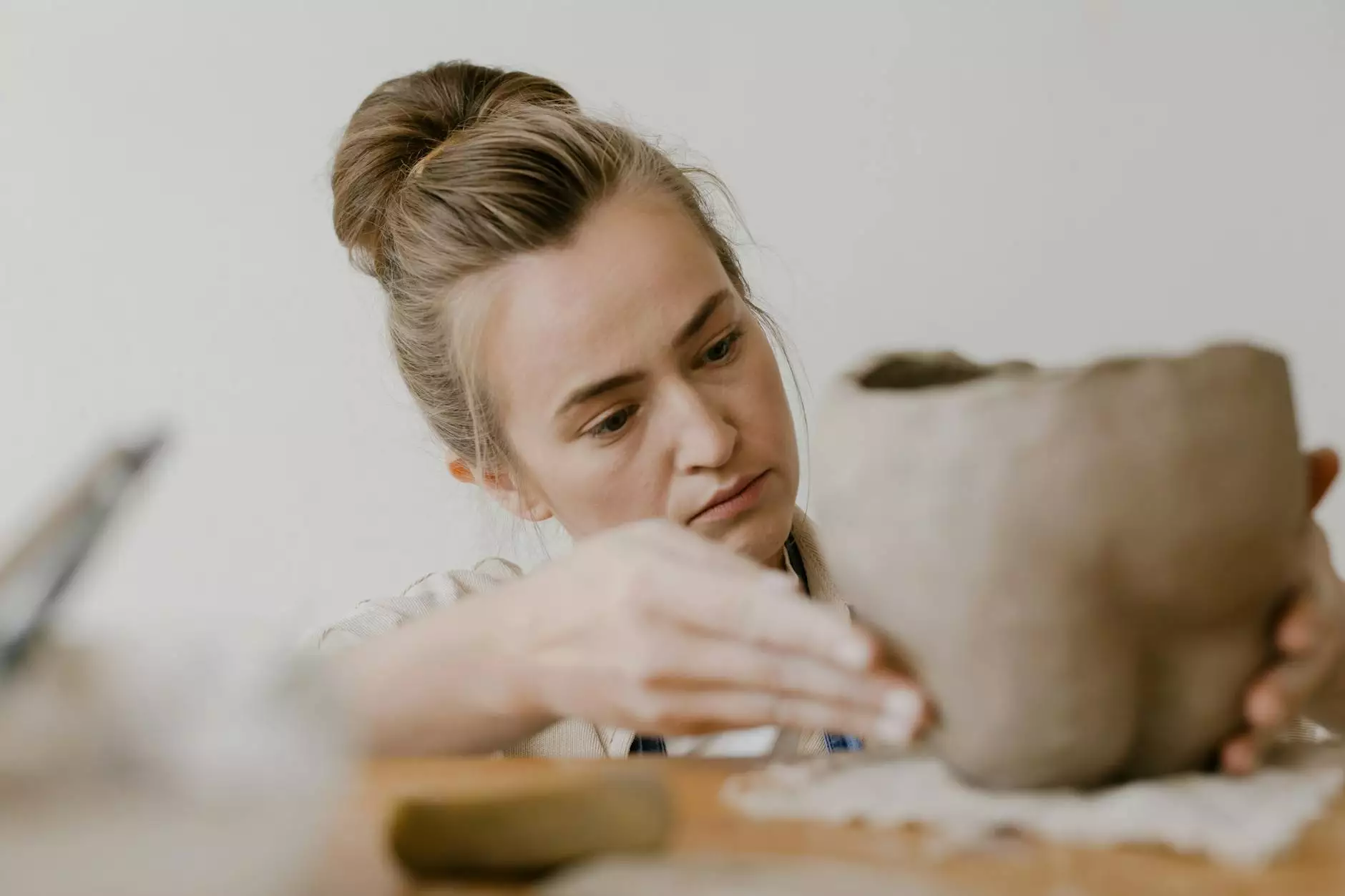
In the contemporary landscape of manufacturing, precision and efficiency have become paramount. One of the key players in achieving these standards is the die casting mold company. This article delves deep into the world of die casting, explores the intricacies of mold design and manufacturing, and highlights the significance of these companies in providing superior metal fabrication services.
What is Die Casting?
Die casting is a metal casting process that involves forcing molten metal under high pressure into a mold cavity. This process is typically used with non-ferrous metals, especially alloys of zinc, aluminum, and magnesium. The result is highly complex shapes with excellent dimensional accuracy, smooth surfaces, and minimal post-production work. These attributes make die casting a favored choice across various industries.
Types of Die Casting Processes
There are primarily two types of die casting processes used in the industry:
- Hot Chamber Die Casting: Ideal for metals with low melting points, the hot chamber method involves keeping the melting pot and the die chamber interconnected at all times, facilitating quick cycle times.
- Cold Chamber Die Casting: This method is used for metals with high melting points. The molten metal is poured into a chamber that is separate from the furnace, which means it requires more energy and time for each cycle.
Why Choose a Die Casting Mold Company?
Partnering with a reputable die casting mold company offers manufacturers numerous advantages. Here are some key reasons:
- Expertise in Design: Specialized in creating detailed and complex mold designs, die casting companies employ skilled engineers who utilize advanced CAD software to ensure precision and efficiency.
- Quality Assurance: A reliable mold company adheres to strict quality control processes, ensuring that the molds produce consistent and high-quality parts every time.
- Cost-effectiveness: While the initial investment in molds may seem high, die casting significantly reduces material wastage and production time, leading to long-term savings.
- Scalability: Die casting is ideal for mass production, allowing companies to scale up production seamlessly without sacrificing quality.
The Mold Design Process
The mold design process is a critical step for a die casting mold company. It involves several stages:
1. Conceptualization
It begins with understanding the client's requirements, including the intended use of the component, materials, and desired finish. Close communication with the client ensures that all specifications are met from the start.
2. CAD Design
Using Computer-Aided Design (CAD), engineers create 3D models of the molds. This stage allows for the visualization of the final product, and any necessary adjustments can be made before moving to the prototyping phase.
3. Prototyping
Creating a prototype is essential. It is often produced using rapid prototyping techniques, enabling quick feedback and modifications before the actual production of molds.
4. Mold Manufacturing
Once the prototype is approved, the actual molds are manufactured. This phase entails precision machining and assembly, ensuring that every piece fits perfectly and operates efficiently.
Materials Used in Die Casting Molds
The choice of materials in die casting molds plays a significant role in the overall effectiveness of the process. Typically, the following materials are utilized:
- Steel: High-quality steel is used for durability and longevity. It is the most common material for die casting molds due to its strength and resistance to wear.
- Aluminum: Lightweight and less expensive than steel, aluminum molds are easier to handle and suitable for lower production runs.
- Copper Alloys: Known for excellent thermal conductivity, copper alloys are often used in molds that require quick cooling and heating cycles.
Benefits of Die Casting in Various Industries
Die casting is not confined to a single industry; its versatility allows it to play a crucial role in multiple sectors, including:
Aerospace
In the aerospace industry, precision parts are essential. Die casting enables the production of lightweight yet robust components that meet stringent safety and performance standards.
Automotive
The automotive sector heavily relies on die casting for manufacturing various parts, such as engine blocks, transmission cases, and structural components. Die casting enhances fuel efficiency and performance through lightweight parts.
Electronics
With the rising demand for consumer electronics, die casting provides the necessary precision for producing housing and structural components that protect sensitive electronic parts.
Medical Devices
The medical industry benefits from the tight tolerances and complex geometries achievable with die cast parts, which are crucial for creating reliable medical devices.
Environmental Considerations in Die Casting
As industries shift toward sustainable practices, die casting offers a more environmentally friendly option compared to other metal fabrication methods:
- Material Efficiency: Die casting minimizes material waste by using only the necessary amount of metal to produce parts.
- Energy Efficiency: The ability to produce large quantities of parts quickly reduces energy consumption.
- Recyclability: Many metals used in die casting, like aluminum, are highly recyclable, promoting a circular economy.
The Future of Die Casting Mold Companies
As technology advances, the future of die casting mold companies looks promising. Innovations in materials, automation, and design software will continue to enhance the capabilities of die casting.
Furthermore, with the increasing demand for sustainable practices, companies that specialize in environmentally friendly die casting methods will likely gain a competitive edge in the market.
Conclusion
The importance of a die casting mold company in the manufacturing landscape cannot be overstated. By leveraging advanced technology, skilled workforce, and sustainable practices, these companies not only deliver high-quality components but also contribute to the overall efficiency and effectiveness of their clients’ production processes. As industries continue to evolve, die casting will play an increasingly vital role in shaping the future of manufacturing.